مدل مدیریت دارایی فیزیکی؛
راهی به سوی حذف اتلافهای آشکار و پنهان شرکتها
علی سعیدی، کارشناس خبره صنعت برق و دبیر انجمن صنفی کارفرمایی شرکتهای توزیع نیروی برق کشور
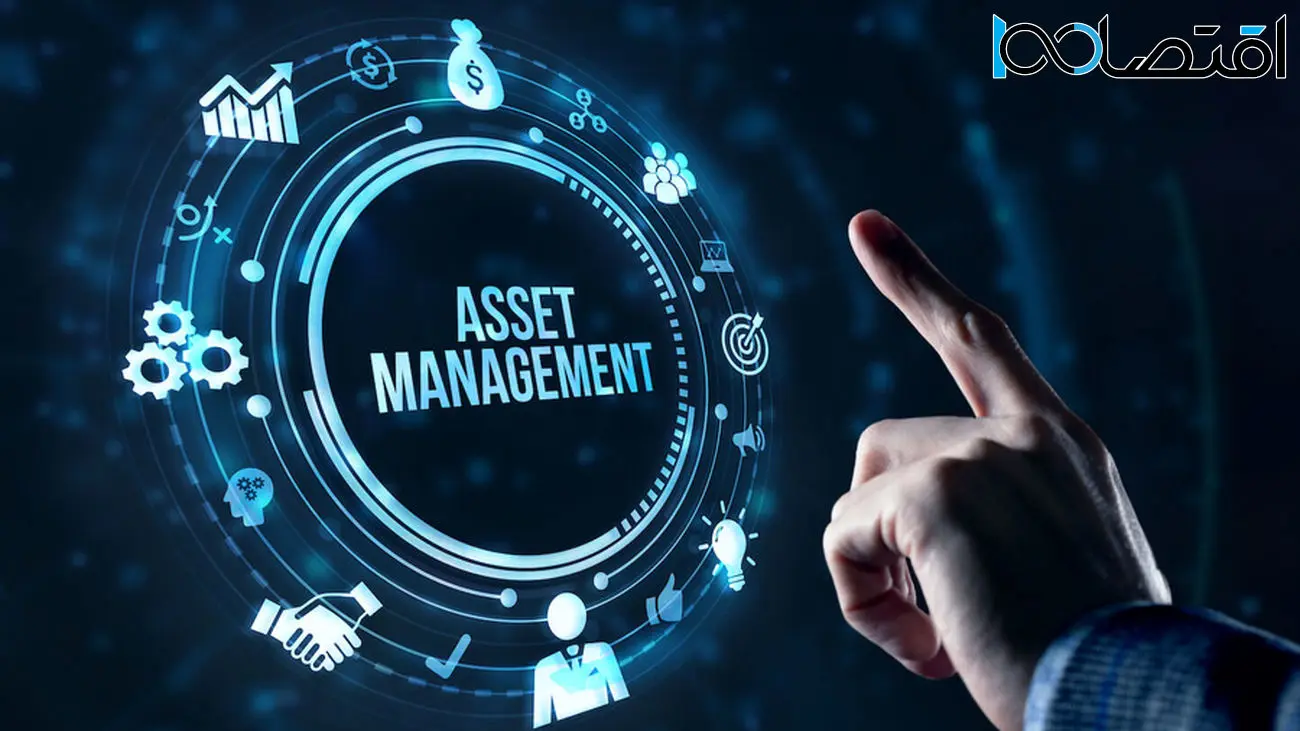
عبارت «چرخه خبیث اتلاف» عبارتی است که در کتاب «راه تویوتا» از آن یاد شده و نشان میدهد که از دید سیستم تویوتا، اتلاف آنقدر بد و منفور بوده و اثرات ضد اقتصادی و اجتماعی داشته که از آن به عنوان «چرخه خبیث اتلاف» یاد شده است.
شرکت تویوتا در سیستمی که پیاده کرده، مدعی است که مطلقا اتلاف ندارد و با مطالعه کتاب «راه تویوتا» انسان درمییابد چقدر دقیق اتلافها را شناسایی و آن را حذف کردهاند. آنها حتی اتلافی را که در مسیر جابهجایی یک کالا یا یک قطعه توسط کارگر اتفاق میافتد را از نظر دور نداشتهاند.
حال، به نظر نگارنده، اگر با دید بهرهوری و کشف اتلافها به اطراف خودمان و نحوه انجام فرایندهای کاریمان نگاه کنیم، به سادگی متوجه میشویم که متاسفانه همه ما در تمام ارکان کشور گرفتار «چرخه خبیث اتلاف» هستیم.
شاید بتوان گفت ما بهطور کلی گرفتار باتلاق اتلاف شدهایم و متاسفانه هیچ حرکت اصلاحی هم مشاهده نمیشود و هر روز در این باتلاق بیشتر غرق میشویم.
«اتلاف»هایی که حل آنها به هیچ وجه از تحریمهای ناجوانمردانه تاثیر نمیپذیرد و حل آنها فقط وابسته به عزم و اراده و البته دانش مدیران ارشد سازمان و جسارت آنها برای تحول و تغییر فرایندها، است.
حتی و حتی، اگر فرضا، این تنگناها و اتلافها ناشی از تحریمهای ناجوانمردانه باشد، باید به گفتههای رهبران کشورهایی که کشورشان را از این گونه تنگناهای شدید عبور دادهاند، تمسک جوییم و با اتکا به توان مدیریتی و اراده تحولخواه و جسورانه آنها به رفع آنها بپردازیم.
این رهبران گفتهاند:
«بحرانها و تنگناها، بزرگترین مدرسه هستند»
به شرطی که مدیران آن کشور و یا سازمانها، عزم استقلال و بهرهوری داشته باشند. مطالعه سرگذشت «شرکت تویوتا» و ... عبرتآفرین است و میتواند چراغ راهی برای مدیران کشور باشد.
قبل از پایان این مقدمه، مصرا مایلم نتیجه وحشتناک اتلافهایی که متاسفانه در کشور ما ایران، اتفاق میافتد به زبان اقتصادی بیان کنم. این آمار از سوی یکی از مشاوران مطرح ایرانی که در سطح بینالمللی فعالیت میکند بیان شده است.
این آمار به مانند تلنگری بزرگ باید مدیران را بیش از پیش به خود بیاورد تا منشا حرکتی برای حذف «اتلافها» و «بدکاریها» و «دوبارهکاریها» و در یک کلمه ارتقای بهرهوری شود:
در کشور ایران، حدود 1000 میلیارد دلار تجهیزات صنعتی و علاوه بر آن حدود 2000 میلیارد دلار ساختمان و ابنیه موجود دارد.
متوسط عمر ساختمانها و ابنیه در ایران در خوشبینانهترین حالت حدود 40سال بوده، در حالی که در کانادا 100 سال است.
با این حساب، سهم هزینه نگهداری و استهلاک ساختمانها و ابنیه در ایران سالانه حدود 50 میلیارد دلار می شود در حالی که همین هزینهها در کانادا سالانه 20 میلیارد دلار است.
به عبارت دیگر ما در سال حدود 30 میلیارد دلار در اثر عدم طراحی درست و عدم نگهداری و تعمیرات درست، متحمل زیان میشویم.
در این حالت جالب است بدانیم که درآمد فروش نفت ایران در شرایط غیر تحریم، با صادرات روزانه دو میلیون بشکه و با قیمت هر بشکه 50 دلار سالانه حدود 30 میلیارد دلار میشود!!!
یعنی ما در اثر «طراحی نادرست» و «نگهداری و تعمیرات غیر علمی» به دلیل «عدم اصلاح سازوکارها و عدم اصلاح فرایندها» تمامی درآمد ناشی از فروش نفت را هدر میدهیم!!!
به این ترتیب مشخص میشود که اگر کشورمان از فرایندهای علمی بر اساس مدلهای علمی کاربردی برای «طراحی فنی درست» و «نگهداری و تعمیرات درست» برخوردار باشد، کشور دیگر به پول نفت نیازی ندارد و میتواند «آقایی» کند و از همه مهمتر «غیر قابل تحریم» شود.
اتلافهایی که باعث این خسران عظیم در کشور شده، مربوط به تمام ارکان اجرایی و تصمیمگیری کشور و قطعا قسمتی از این اتلافها مربوط به مدیران بخش برق کشور است.
به ضرس قاطع باید قبول کنیم که این اتلافها مجموعهای از اتلافهای بزرگ و کوچک هستند. و باید به موازاتی که برای اصلاح فرایندهای اتلافآفرین بزرگ کار میکنیم، برای اصلاح فرایندهای اتلافآفرین کوچک هم کار کنیم و به هیچ عنوان اتلافهای کوچک را به دلیل این که کوچک هستند، دست کم نگیریم.
یکی از مصادیق بارز اتلافهای آشکار و پنهان در مجموعههای صنعتی تجهیزمحور مانند صنایع فولاد، خودروسازی پالایشگاهها و نیروگاهها و شبکههای انتقال و توزیع برق، پتروشیمی، مخابرات و نیروهای مسلح و ...، وجود فرایندهای سنتی مربوط به امر مهم نگهداری و تعمیرات در این صنایع است که نوعا مبتنی بر انجام تعمیرات اساسی بر روی تجهیزات در فواصل زمانی ثابت (PM) است.
این در حالی است که امروزه در مقوله مدیریت داراییهای فیزیکی، موضوع نگهداری و تعمیرات صنایع تجهیزمحور بر اساس RCM (Relaability centered maintenance) یعنی نگهداری و تعمیرات مبتنی بر قابلیت اطمینان شکل گرفته است.
در کتاب «نگهداری و تعمیرات مبتنی بر قابلیت اطمینان» تالیف John Moubrary و ترجمه دکتر زواشکیبایی و مهندس آزادگان آمده است:
«روش نگهداری و تعمیرات مبتنی بر قابلیت اطمینان (RCM) فرایندی سیستماتیک و علمی برای تعیین فعالیتهایی است که برای حصول اطمینان از ادامه کارکرد تجهیزات و بهطور کلی دارایی های فیزیکی مطابق با انتظاراتی که از کارکرد آن تجهیزات داریم، باید انجام شود.
RCM که از نظر اغلب متخصصان نگهداری و تعمیرات بعنوان اثربخشترین روش نسبت به هزینههایش برای ایجاد و توسعه استراتژیهای نگهداری و تعمیرات در سطح جهانی شناخته میشود، که باعث دستیابی سریع به بهبودهایی پایدار و معتبر در زمینه دسترسپذیری و قابلیت اطمینان کارخانهها، کیفیت محصول، ایمنی و سلامت محیط زیست میشود.
RCM را شاید بتوان توانمندترین ابزار تعریف فعالیتهای نت (نگهداری و تعمیرات)، تعیین فواصل انجام آنها، و نحوه اجرای آنها دانست. این ابزار که برای اولین بار در صنایع هوایی آمریکا ایجاد شد، توانست میزان سقوط های متاثر از نقص فنی هواپیماهای مسافربری را از حدود 40 سقوط در یک میلیون پرواز به حدود 0.1 سقوط در یک میلیون پرواز کاهش دهد. برای راحتتر شدن درک موضوع باید گفت که اگر این کاهش چشمگیر 400 برابری صورت نمیگرفت امروزه ما باید انتظار سقوط یک هواپیمای 747 در هر روز را میداشتیم.
همین موفقیت اعجابآور باعث شد که امروزه RCMII که نسخه طراحیشده برای صنایع عمومی RCM اولیه است در همه صنایع و اکثر کشورها پیادهسازی شود. آهنگ پیادهسازی RCMII در طی سالهای اخیر نهتنها کُنده نشده، بلکه شدت نیز گرفته و موفقیت آن مدیون فوایدی است که این ابزار برای سازمانها به ارمغان آورده است.
مهمترین فواید پیادهسازیRCMII را شاید بتوان در شش گروه کلی طبقهبندی و خلاصه کرد:
افزایش قابلیت دسترسپذیری دستگاهها و ظرفیت تولید
کاهش هزینههای نت، خرابی دستگاهها و عملیاتی
کاهش چشمگیر حوادث صدمهزننده به ایمنی و محیط زیست
افزایش طول عمر تجهیزات
کاهش قابل توجه فعالیتهای اضطراری سازمان
ایجاد فرهنگ همکاری در بین همه گروهها و همچنین فضای برنامه ریزی و عملکردی پیش اقدام، این فرهنگ تنها به واحد نت (نگهداری و تعمیرات) محدود نمیکند، بلکه در سایر واحدها از قبیل عملیات، مهندسی، تامین قطعات یدکی شکل گرفته و در نهایت به کل سازمان تسری مییابد.
هرجا شرکتی تاکتیکهای نگهداشتی را به کار گیرد که با استفاده از رویکردهای سنتی و بدون بهرهگیری از RCM تدوین شدهاند، دستش از تعالی کوتاه میماند، گاهی بسیار کوتاه. گاهی این شرکتها با RCM و دیگر شیوههای بهینهسازی آشنایی ندارند، ولی عمدتا آگاهانه از سرمایهگذاری در این زمینه اجتناب میکنند؛ زیرا از ارزش واقعی این شیوهها اطلاع ندارند. شرکتها عموما رویکردی کوتاهمدت را انتخاب میکنند که نتایج کوتاهمدت را برایشان به ارمغان بیاورد. در شرکتهایی که این طرز فکر بر آنها حاکم است، همیشه به راحتی میتوان انواع حالات خرابی را یافت که نادیده گرفته شدهاند یا تاکتیکهایی را دید که این حالات خرابی را به شیوهای اشتباه مدیریت کردهاند و غالبا فعالیتهای نگهداشت بسیار بیشتر از میزان نیاز است. این اقدامات خیرخواهانه که به سرعت به تدوین برنامههای PM میانجامد، غالبا در بهبود عملکرد قابلیت اطمینان ناکام میمانند، به ندرت موجب کاهش هزینهها میشوند و اعتبار واحد نگهداشت را نیز خدشهدار میکنند، چرا که نمیتوانند بهبودهای وعدهشده برای کسبوکار را محقق کنند. اثربخشترین برنامه های نگهداشت با استفاده از RCM و در مرحله طراحی ایجاد میشوند تا مناسبتترین تاکتیکها را برای هر وضعیت و شرایط عملیاتی و محیطی تعیین کنند. از روش RCM هم در مرحله طراحی و هم پس از ورود تجهیز به عملیات به خوبی میتوان بهره گرفت. این روش، کاملترین روش موجود برای تعیین الزامات برنامه نگهداشت است و به شدت توصیه میشود، به ویژه اگر پیامدهای خرابی شامل ریسکهای ایمنی، زیستمحیطی و افت شدید کسبوکار شود.
مدیریت قابلیت اطمینان به طور خلاصه به معنای پیشینهسازی زمان در دسترس و کمیتهسازی بسامد حوادثی است که به توقف منجر میشوند. مزیت اصلی مدیریت قابلیت اطمینان این است که با افزایش میانگین زمان بین خرابیها (MTBF)، قابلیت اطمینان دارایی را افزایش میدهد که به افزایش دسترسپذیری، ظرفیت تولید بیشتر و درآمدزایی منجر میشود. همچنین افزایش قابلیت اطمینان، کاهش هزینه را به دنبال دارد؛ زیرا تعمیرات پرهزینه و مدت زمان توقفاتی را که به افت تولید منجر میشوند، کاهش میدهد.»
از طرفی چشمانداز جهانی صنعت برق در سال 2025 میلادی میگوید در قرن بیستویکم اگر کشوری میخواهد اقتصاد و صنعت پویایی داشته باشد باید قابلیت اطمینان سیستم برق آن کشور آن چنان بالا باشد که بتواند در قرن دیجیتال، صنعت و اقتصاد دیجیتال خود را با رویکرد حفظ محیط زیست بر مبنای هوشمندی شبکهها پشتیبانی کند.
این در حالی است که اگر واقعبینانه بخواهیم به عملکرد صنعت برق کشور نگاه کنیم باید بگوییم که:
با وجود همه تلاشها و سختکوشیها، متاسفانه صنعت برق کشور با شاخص های جهانی فاصله معناداری دارد.
یعنی شاخص SAIDI کشور اصلا قابل قبول نیست و شاخصهای محیط زیست و هوشمندسازی شبکهها هم وضع نامناسبی دارد.
اینک با توجه به تجارب جهانی در مبحث «نگهداری و تعمیرات» صنایع تجهیزمحور، یکی از مواردی که صنعت برق اعم از بخش تولید و بخش انتقال و بخش توزیع باید به فوریت به آن سمت حرکت کند، استقرار «سیستم مدیریت داراییهای فیزیکی» است.
«مدیریت داراییهای فیزیکی» در صورت استقرار در شرکتهای تولیدکننده برق و شرکتهای انتقال و شرکتهای توزیع برق و بهکاربردن روشهای RCM و RCA (Root cause Analysis) و سایر روشهای مندرج در مدیریت داراییهای فیزیکی آنچنان شرکتهای فوق را چالاک و بهرهور میکند که پس از استقرار آن، گروههای آچار بهدست و واحدهای نت (نگهداری و تعمیرات) شهد شیرین کار درست در زمان درست و به شکل درست را میچشند و ارمغان حذف اتلافهای پیدا و پنهانی که در مسیر قبلی نگهداری و تعمیرات وجود داشت را به چشم خواهند دید.
نگارنده که در زمینه استقرار مدیریت داراییهای فیزیکی در شرکت توزیع (که از قضا استقرار این مدل در بخش توزیع برق نسبت به سایر بخش های تولید و انتقال برق سختتر است) در برق مشهد از سال 93 را در کارنامه خود دارد، با تمام وجود تفاوت انجام نگهداری و تعمیرات در شبکههای توزیع برق را قبل و بعد از استقرار مدیریت دارایی فیزیکی احساس کرده است و از حذف اتلافهای کوچک و بزرگ و پیدا و پنهانی که در مسیر نگهداری و تعمیرات شبکههای گسترده بخش توزیع وجود داشت، لذت برده است و به همین دلیل به تمام شرکتهای تولید برق و شرکتهای انتقال برق پیشنهاد میکنم هرچه سریعتر به سمت استقرار این مدل مدرن جهانی حرکت کند، تا از مزایای آن بهویژه افزایش قابلیت اطمینان نیروگاهها و کاهش هزینههای نگهداری و تعمیرات استفاده کند.
انتهای پیام